Sistema de corte por chorro de agua con robot triple tipo techo Yaskawa GP20
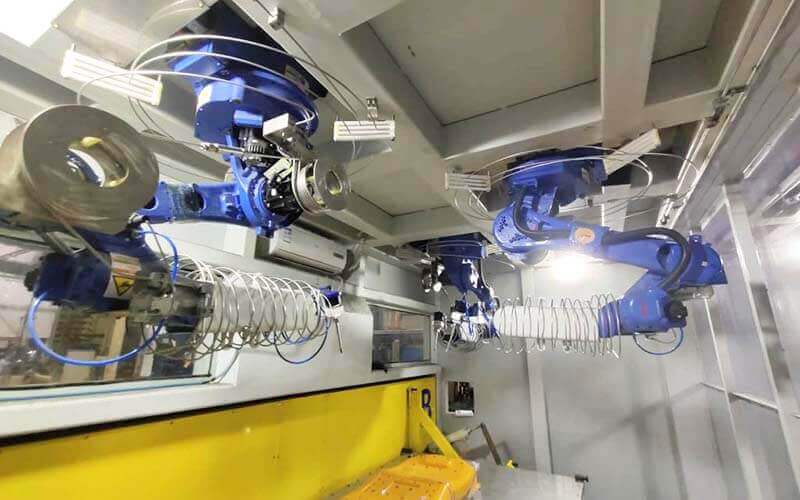
Waterjet cutting combine with robot solutions Shape Process Automation the versatility of waterjet with the smart manufacturing power of automation, increasing manufacturing flexibility, capacity, and output.
Highly Reliable and Path Accurate
Cold Cutting Process (no HAZ)
Hard, Soft or Multi-Layer Materials
Minimal Fixturing
Flexibility to Program Infinite Parts
Increase Throughput with Multiple Robots
Waterjet Cutting Cell | Technology by Shape Process Automation
Depending on your production demands, each of these waterjet cutting system can be supplied with single, dual, triple or quad robot configurations, and if your demands are greater overhead gantries can be configured with up to six robots, paired with a complete UHP plumbing package – from pump to nozzle – sized to meet your production’s waterjet cutting requirements.
Select from a wide range of waterjet cutting cell configurations, such as A-Frame (wall mount), overhead gantry, rotating wall or simple floor mount cells.
1 | Brand of robot arm: | YAKAWA | |
2 | Model: | GP20 | |
3 | Style: | Ceiling | |
4 | Quantity of robot arm: | Tripple | |
5 | Application: | Automotive interior cutting | |
6 | Pump type: | STREAMLINE SL-VI 100HP large-flow rate intensifier pump | |
7 | Oprator required: | 2 sets | |
8 | Customize avialable: | Yes | |
9 | Including devices: | Robot arm, cutting table, high-pressure pump, chiller, control system, etc.. |
The Design and Core Configuration
This is the design of a set of three robot arms with ceiling structure. The ceiling structure robot integration is mostly used in mass-produced automotive interior production lines, and is generally located behind the thermal press.
Ceiling-type robot waterjet cutting has a fixed-structure cutting platform. Such a cutting platform is generally suitable for cutting large automotive interior parts such as headliners.
It can be cut one at a time, but the design of three robot arms makes simultaneous cutting very efficient. The front and rear doors of the robotic shape process automation are the locations for loading and unloading materials.
Two operators, one operator is responsible for taking the material off the cutting table and removing excess material after cutting.
Another operator removes the material from the heat press at the rear door and places it on the robotic waterjet workstation.
This is a link that exists in the middle of the entire production line. But the robot waterjet cutting process basically ranks behind.
After the automotive interior parts undergo the shape process automation, they only require an inspection by the operator. Then hang it up and wait for a few hours before can use it normally.

Core Configuration of Waterjet Cutting cell
1: Ceiling Enclosed Working Station
2: YASKAWA GP20 robot arm
3: Equipped with SL-VI 100HP large-flow rate intensifier pump
4: High-performance industrial chiller, the whole set of equipment can works well in hot areas
5: The powerful vacuum adsorption system keeps the cutting parts firmly fixed on the cutting table
6: Sistema de purificación de agua, que puede prolongar la vida útil del orificio.
7: Sistema de protección de seguridad para detectar personal en el área de trabajo y proteger la seguridad del personal.
8: sistema de control general
STREAMLINE SL-VI 100HP large-flow rate intensifier pump
WINWIN robot waterjet cutting system customize for our customer requirment, which is carried out under the circumstances of the customer’s initial factory construction or capital budget.
The first step is for the customer to choose to purchase a single-arm robot waterjet cutting workstation, but a set of installation interfaces are reserved in the control and other structural design.The customer chose the SL-VI 100HP high-flow intensifier pump. We all know that KMT is a very famous high-pressure pump manufacturer in the world, and WINWIN’s pump quality is comparable to it.Our design idea is that the customer first installs a set of robotic arm waterjet cutting workstations.

If the customer needs greater productivity in the future, we will easily install a robotic workstation, which will double the productivity.Moreover, during the initial installation, various installation needs for adding the robot system in the later period have been reserved. In the end, the two sets of robots can share a high-voltage system.
And the two sets of robots can be operated relatively independently. This solution not only increases productivity, but also allows for multiple cutting table positions in the future.This means that parts for many different car interior models can be cut at the same time, doubling the flexibility.
Not only that, there is a greater guarantee in terms of failure rate. If one robot integration requires maintenance, it will not affect the normal work of another robot workstation, ensuring 24-hour operation.
In this plan, the large-flow intensifier pump we equip our customers is very important. Let’s take a look at the parameters and advantages of this high-pressure system.

Features of Servo Motor SCREAMLINE SL-VI(100HP)
1. Servo Motor to Oil Pump, Power-Cost 15% Reduction
2. Stable Working Pressure, Fast Reaction, Low Fluctuation of Waterjet Pressure
3. Dual Intensifier Design, Alteration-Work Mode, Suitable to 24/7 continuous working
4. Variable Pump with 2L Attenuator, Stable Working Pressure, Extending service life of Accessories.
5. Noise <63 dbs. Better Working Environment.
6. Comprehensive fault detection and troubleshooting, real-time monitoring of important values such as pressure, speed, hydraulic oil level, etc.
7. Can support Max. 6 pieces of Orifices, improving the working efficiency.
8. Double Oil-Filtration at Oil Pump Inlet and Return Port, keep on good quality Oil.
WINWIN robot waterjet cutting system not only focuses on quality and technology, but also attaches great importance to after-sales service. WINWIN flies directly to customer sites around the world for after-sales service, installation and training. If you also have needs for robot waterjet cutting cell, come and consult us!